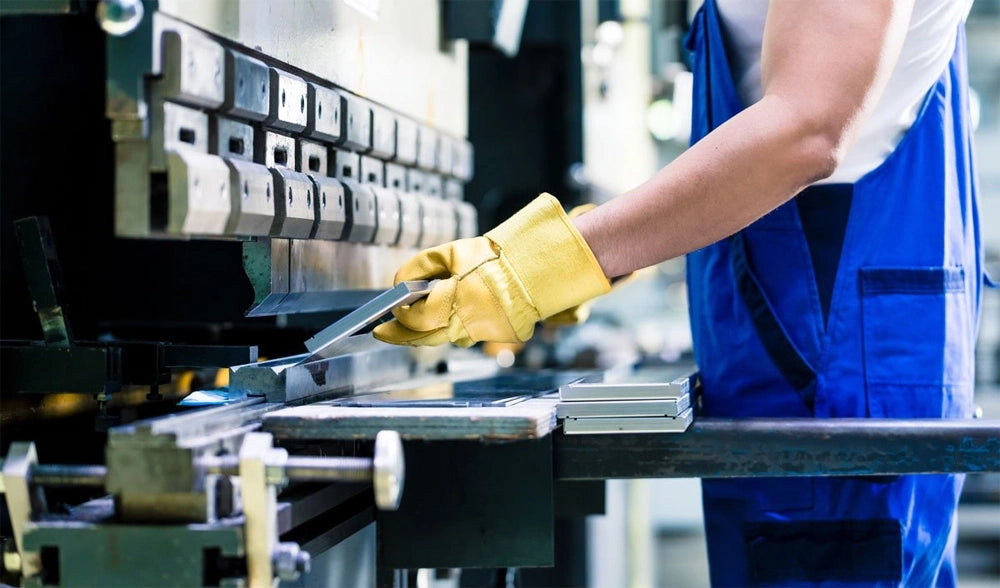
The Many Advantages of Custom Manufacturing
Share
In the past, companies faced limited options for producing their goods: costly on-site manufacturing or outsourcing to third parties. However, this landscape has dramatically evolved. The emergence of custom manufacturing has revolutionized production, alleviating many challenges associated with traditional manufacturing methods.
But what exactly is custom manufacturing, and why is it highly esteemed in modern processes? Uncover these insights and more as we explore some of the world's prime locations for custom manufacturing.
What Is Custom Manufacturing?
Initially, the industrial boom grappled with manufacturing issues, but over time, companies worldwide have struck a balance between internal production and contracting work externally. Custom manufacturing is the key, especially when bespoke parts or made-to-order products are essential.
Essentially, it involves engineering, designing, and fabricating products based on unique specifications, encompassing built-to-order parts, one-off runs, short production runs, and mass customization. Entities engaging in this practice are often referred to as OEM companies (original equipment manufacturers). While closely associated with the automotive and IT sectors, the scope of OEM manufacturing extends limitlessly.
Custom Manufacturing vs. Mass Production
Contrary to the mental image of massive factories churning out identical parts, custom manufacturing deviates from mass production. The latter focuses on utilizing significant raw materials to rapidly produce large quantities of items. In contrast, custom manufacturing emphasizes streamlined processes, effectively producing smaller quantities of goods in shorter timeframes.
The distinction lies not only in the quantity of raw materials used but also in the diversity and uniqueness of the produced goods. Mass production operates on a larger scale, consuming more time, materials, labor, and space, whereas custom manufacturing, while smaller in scale, often proves to be more efficient.
The production line stands out as a critical element distinguishing mass production. In this setup, large quantities of items are manufactured with minimal direct involvement from factory workers, enabling a continuous assembly line. Custom manufacturing may adopt similar principles but involves fewer personnel and equipment. The objective is to assist clients in crafting their goods in tailor-made ways, prioritizing efficiency despite smaller-scale production.
Prototyping and Production: Key Divisions
Custom manufacturing encompasses two primary divisions: prototyping and production, both integral to the process. Prototyping, also known as "mock-up manufacturing," holds immense value. It involves testing, evaluating, or altering a part or component before its integration into the final project. This phase aids in cost and time savings for both you and your company. For instance, when dealing with complex designs like aircraft wings, a custom mock-up can preemptively address potential issues.
On the other hand, production or "serial production" refers to businesses manufacturing products in larger quantities, often for commercial purposes. Although these products can be custom-made, they are produced on a larger scale. For instance, car companies might utilize custom manufacturing to produce limited quantities of parts for older vehicles, deviating from their mass production strategies for new car models.
The Pinnacle Benefits of Custom Manufacturing
While mass production and in-house manufacturing possess advantages, the merits of custom manufacturing outweigh these methods. As a service, custom manufacturing excels in accommodating material variations, adapting to changing design requirements, and offering unique finishing options. It serves as an ideal solution for items that cannot be mass-produced due to their specific nature. Here's why it stands out:
Tailored Products: Custom manufacturing allows extensive customization, ensuring exact specifications are met, ultimately enhancing the quality of the end product. This eliminates settling for the closest alternative on a mass-produced lineup.
Enhanced Efficiency: OEM manufacturers deliver precise, high-quality products, resulting in reduced wastage and fewer production failures. This efficiency saves time and resources by eliminating the need for rework or returns.
Unparalleled Accuracy: Custom manufacturing processes prioritize accuracy by eliminating waste and ensuring uniformity among products in terms of size, shape, or material. Expert teams equipped with high-quality machining capabilities contribute to this precision.
Cost-effectiveness: Despite initial perceptions of higher costs, custom-made items are often 50-75% cheaper compared to similar mass-produced items due to reduced waste and associated expenses.
Reduced Lead Times: Custom manufacturing involves fewer processes, streamlining design processes and eliminating waiting periods for pre-made components, resulting in shorter lead times.
Quality Control: Continuous monitoring throughout the process enables prompt identification and rectification of defects, crucial for maintaining stringent quality standards.
Design Flexibility: Unlike mass production limitations, custom manufacturing offers freedom in material and technology usage, enabling the creation of a wider range of innovative products.
Increased Sales and Customer Loyalty: Customizable products often yield higher customer retention and increased sales due to personalized offerings, fostering a sense of involvement in the purchase process.
Scalability and Inventory Management: Starting small with custom manufacturing allows scalability without the burden of excess inventory, offering flexibility in adjusting to varying demands.
Selecting a Custom Manufacturer
Choosing the right manufacturer for your project is crucial for success. Factors to consider include:
● How long have they been in this industry?
● How about their testimonials?
● Do they have clear and efficient website?
● Are they easy to talk with?
● How about their logistical support?
Setting clear goals and expectations from the outset is essential for a productive partnership. Flexibility in adapting to changes during the customization process is also vital, emphasizing effective communication and trust in their expertise.
Identifying a Quality Manufacturer
Evaluating a potential manufacturer involves asking them the following questions:
● Do they use quality materials?
● Is their business transparent for clients?
● Do they have any insight into their product development?
● How do they treat improvements and prototypes?
● Is their process customizable?
● Can they work with you from the start to the finish?
A reputable partner will prioritize quality control to ensure compliance with specifications and safety standards.
Conclusion
In conclusion, the significance of custom manufacturing cannot be overstated. Its ability to deliver precise, tailored products with enhanced efficiency and flexibility makes it a cornerstone of modern production methodologies. Choosing the right manufacturer, based on clear communication, trust, and a shared vision, is instrumental in leveraging the myriad benefits custom manufacturing offers.
Is your business looking to a bulk purchase of Ozone Generators and Ozone-Related Equipment? Or are you seeking to work with a reliable supplier? If this is the case, please Contact Us immediately and see what we can do together.